With hardware developments being slower in their evolution, it fell to software at this year’s drupa to wave the flag of improving efficiency, workflow and ultimately costs. In this software feature, we highlight some of the upgrades available to your business right now.
Kicking things off with their drupa launch was eProductivity Software (ePS) and its latest cloud-based print Management Information System (MIS) solution, Nubium. Purpose-built for small to medium commercial printers, ePS are pitching Nubium at print and packaging companies.
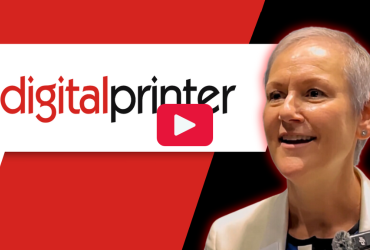
Charlotte Tueckmantel, ePS chief operating officer, explains the company’s new MIS solution, Nubium, in this latest video
Nubium’s architecture and intuitive tools are designed specifically for printers who require an MIS with low maintenance and overhead. As a 100% cloud-native MIS, Nubium enables rapid startup and onboarding, allowing businesses to support a wide range of products and services almost immediately from the start.
Offering seamless integration with web-to-print eCommerce platforms such as MarketDirect StoreFront, Nubium aims to enhance the overall customer experience by streamlining online order processing and production workflows. The integration is a versatile and essential tool for commercial printers looking to optimise their entire business process from online orders to financial management.
Key features and benefits of Nubium include advanced estimating, allowing precise and efficient quoting and automated machine and process selection. Inventory management gives users the ability of comprehensive management of raw materials and finished goods, optimising stock levels and reducing waste. Nubium will also seamlessly integrate with accounting tools like QuickBooks ensuring streamlined financial operations. Lastly, the scalability of the product enables businesses scale-up, ensuring you always have the right tools without significant upfront investment.
Another software specialist with a presence at drupa were Fiery. Their latest offering focuses on the next generation of its sign making and graphic production software, SignLab 11. This latest release combines powerful vector and bitmap design and editing tools to help simplify the production of banners, signs, decals, décor, and more. From one platform, sign businesses can design and produce vibrant and unique digitally printed, vinyl cut, and print/cut signs and graphics.
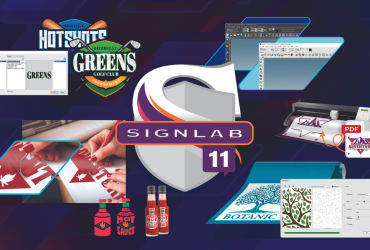
Fiery’s SignLab gets an upgrade to version 11
Fiery believe that unlike general design platforms, SignLab is purpose-built for the production environment, offering greater control of design elements and support for the most popular print, cut, and hybrid devices. The new vectorisation controls, weed features, pdf cut tools, effects catalogue, and fit to shape features are not typically found in general design applications and require third party applications. Combining these tools with the widest direct support for output devices, SignLab provides printers with a comprehensive and feature-rich production platform that includes integrated design, layout, and production workflow software for sign making, large format graphics, and print/cut applications.
SignLab 11 features a number of updated tools, such as Vectorization Previewer which eliminates guesswork using a new live preview of vectorisation controls before applying them to an object. The Fit To Shape tool allows designers to customise text shapes and layouts effortlessly by automatically adjusting text to fit any vector shape, while the Effects Catalogue can help save production time by harnessing a library of commonly applied effects such as shadows, gradients, colour combinations and apply saved effects to new objects in a single click. Also on hand is the Power Weed Text Lines feature, allowing faster and easier vinyl weeding with less margin for error, which automatically positions weed cut lines amongst text and graphics for an efficient weeding process. Fiery promote that this feature saves manual labour and reduces waste by adding all weed cut lines to a design reducing guess work with optimal placement.
With an eye on an industry facing modest growth and tight margins, software developer Enfocus has updated its PitStop programme with PitStop 24.07. Providing affordable, flexible automation tools for file handling, Enfocus specialises in helping printers operate more efficiently. With a suite of tools designed to automate repetitive tasks, streamline operations, and reduce waste, their mission is to support printers to enhance their productivity by giving them back their most valuable resource – their time – with quality control being top of the agenda. Failed jobs waste time, resources and increase material waste and with the remote nature of the modern printing workplace meaning teams often find themselves sharing documents across multiple users or sites. This introduces the possibility of mistakes creeping in, particularly if remote teams are working across different versions of settings.
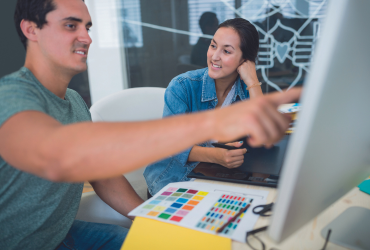
Enfocus’s PitStop gets an update this year to version 24.07
PitStop 24.07 overcomes these challenges and can enhance productivity by synchronising resources through the Enfocus Cloud. With its new Resource Syncing functionality, this platform facilitates effortless real-time sharing of Preflight Profiles and Action Lists across the print production process, removing reliance on email sharing or cloud services to share resources. This cuts complexity out of the process, keeps teams connected, and ensures any changes are immediately propagated. As a result, users can increase the consistency of their printing and benefit from heightened efficiency.
The latest update to PitStop also introduced the ability for users to export images directly to TIFF format, removing the need for external conversion tools. The program fully supports colour spaces and ICC profiles, and the PitStop Server CLI can also be used to generate TIFF files.
Also, from the Enfocus portfolio is Switch. Another tool that can help printers take the busy work out of menial day-to-day tasks, Switch automates them so printers can get on with the activities that matter most. Managing workflows and directly integrating software and solutions into production stacks, Switch directly contributes to improving efficiency in printing. Recently updated, this tool comes with a suite of new features and enhancements to improve security and boost productivity. These include the introduction of a Proxy Module, which aims to maintain the integrity of production environments by enabling Switch installations to stay offline without losing connection to essential resources. This means critical workflows can continue while still adhering to tight security protocols.
Belgian systems integrator-cum-software developer Four Pees introduced Atomyx earlier this year – a suite of cloud-based software for print production file preparation, management and layout that aims to fill in existing gaps in ‘islands of automation’ to provide greater end-to-end efficiency in job acquisition, production and delivery across disparate hardware and software platforms. To be run as an eponymous company alongside the existing Four Pees business, Atomyx comprises three modules – Prepare, Manage and Layout – that will be offered on a usage-based SaaS (software as a service) basis.
Atomyx Prepare is largely based around the functionality of Callas PDF Toolbox and processes submitted artwork files for production via an API. In addition to pre-flighting or quality control functions, it can also be configured to generate secondary documents such as proof sheets or delivery notes and is seen as a natural partner for e-commerce sites and job submission portals, as well
as being able to integrate with other cloud-based prepress functions.
File management is provided by Atomyx Manage, which Four Pees chief technical officer David Van Driessche said ‘connects platforms, processes and people’ handling ‘all kinds of systems out of the box’. It allows jobs, processes and files to be presented visually via a series of dashboards that can be defined for specific people or job functions to present pertinent information, allowing for human input and control where necessary. It can connect to a wide range of third-party systems, from MIS to web-to-print to press vendors’ production systems, via apps developed by Four Pees/Atomyx and is ready for pilot implementations, according to Mr Van Driessche.
The third module, Atomyx Layout, will optimise job layouts via ganging, step-and-repeat or nesting, as appropriate to the job and output device. No specific timetable was given for its availability.
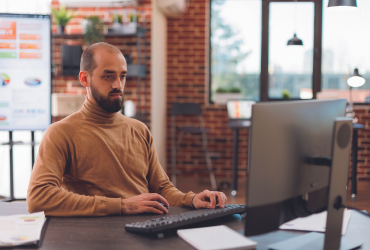
PrintIQ’s cloud-based software allows you the ability to run your business from anywhere, 24/7
Cloud-based MIS platform PrintIQ, allows you the ability to run your business from anywhere, 24/7. Built with flexibility and scalability in mind, the modern approach to print management software is well-positioned to drive growth, offering solutions that caters to both small and large print business.
As a MIS solution specialist in the UK market, PrintIQ’s cloud-based software integrates seamlessly with various print operations, offering a comprehensive suite of tools for workflow automation, job tracking, inventory management, and real-time analytics. With an intuitive interface and robust functionality, it has become a popular choice among print businesses looking to enhance efficiency and reduce operational costs.
With a strong foundation and continuous expansion into the UK market, printIQ is committed to innovation and customer-centric development. Regular updates and new features ensure the software meets evolving industry needs. Additionally, printIQ’s strong support network and training programs help users maximise the system’s potential.