Industry 4.0 is a term that came out of Germany a number of years ago to describe the latest – and fourth – “industrial revolution”, in which automation and data exchange between manufacturing technologies create a “smart factory”. Andy Knaggs looks at how this is already affecting the print sector.
Most printing companies – and I would suggest all of those that want to experience a long and successful future – are deeply interested in the efficiency of their production process.
Their run lengths are shorter than they used to be, the jobs need to be delivered quicker, and they are consequently having to make more frequent job changeovers on printing and post-press equipment, often switching between different formats from one job to the next.
Automated technology and the collection and exchange of data between machines are increasingly providing the answers to this conundrum, delivering efficiency improvements that go way beyond a tweaking of shift patterns or a tub-thumping inspirational speech to machine operators.
This direction for the print industry – and every other manufacturing-based industry – has been given a name: Industry 4.0. It is supposedly the fourth industrial “revolution”, dating back to the original Industrial Revolution in the 18th and 19th centuries. If that was Industry 1.0, then 2.0 was the development of electrical power for motors, lighting and material processing, enabling mass production, and 3.0 saw the rise of computers, the internet and automation.
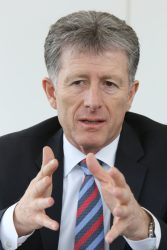
Müller Martini CEO, Bruno Müller, has stressed the global relevance of Industry 4.0
Industry 4.0 takes this further and gives rise to the “smart factory”, where, according to Industry 4.0’s Wikipedia page, ‘cyber-physical systems monitor physical processes, create a virtual copy of the physical world and make decentralised decisions’. Industry 4.0 encompasses cloud computing, robotics, and the Internet of Things, making the analysis and exchange of data between systems and machinery an automatic process requiring little or no human intervention.
It has been approaching for a number of years, and partly it is here now, although there is no doubt much more is to come, and few printing companies will have fully embraced it yet.
The question is should they at least be planning to? Robin Brown, sales manager of Friedheim International’s Digital Solutions division, thinks so: ‘It is incredibly important for UK printers to really embrace the Industry 4.0 concept,’ he says.
‘For our digital customers using Hunkeler finishing lines in conjunction with a continuous [feed] printer, this is already happening and has been for many years. However, greater integration between all processes, whether prepress, printing or finishing, is key for printers moving into shorter, more variable runs, where data is of the utmost importance.’
Bruno Müller, chief executive officer of post-press equipment manufacturer Müller Martini, commented: ‘Industry 4.0 is a global topic that’s of interest to us all. It’s about having an efficient supply chain in order to keep manufacturing costs down despite increasing customisation of products. We can see that the graphic arts industry, owing to the structural change in recent years, has had no choice but to adopt that trend.’
Müller Martini talks not just about Industry 4.0 but the related “Finishing 4.0”, which brings the entire concept more specifically into the print sphere. ‘Finishing 4.0 stands for our solutions, which enable the industrial and cost-effective production of customised print products,’ Mr Müller continues. ‘The aim is to achieve a production system that’s capable of preparing itself fully automatically for a new product based on digital job data, and to launch production without the need for manual interventions, where possible.’
Achieving all of this requires a seamless workflow, a high degree of automation and precise machine engineering, he added: ‘We optimally coordinate those three components and ideally enable a touchless workflow, allowing you to keep your production costs down despite short runs and increased product variety.’
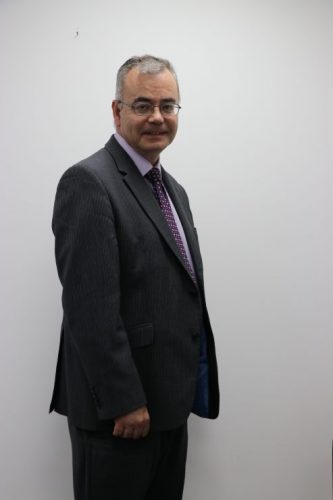
IFS’ technical sales director Jason Seaber foresees a skills shortage
Skills gap
One context to view Industry 4.0 in is the skills shortage in the industry. Jason Seaber, technical sales director at Intelligent Finishing Systems (IFS), sees this as the biggest challenge for printing companies today. ‘Generally, the industry is losing skilled, experienced people and there are very few apprentices coming through. You need automation but with a lower skillset, and without compromising quality. A faster machine that makes an inferior product is not what people want. Moving forward, technology developments will mean fewer operators, but those people can be doing more creative applications and adding value elsewhere in
the business.’
Mr Seaber’s experience suggests that the UK is lagging somewhat behind Germany and France when it comes to Industry 4.0 or “smart manufacturing” technology installations. ‘They are absolutely ahead of us in things like automation and robotic technology. The UK must catch up in the coming years.
The phrase Industry 4.0 is not one that commonly comes up in conversation with customers though, he admits, although most print firms instinctively recognise that the tenets of Industry 4.0 are what they need. ‘They recognise that more and more companies are investing in digital and automated equipment. ‘Most companies know today that to be competitive they need to invest in new automated technology but in post-press it’s not straightforward because there are different types of print finishing. And it’s not just about improving today: they want technology that is flexible and modular so they can adapt it in the future.’
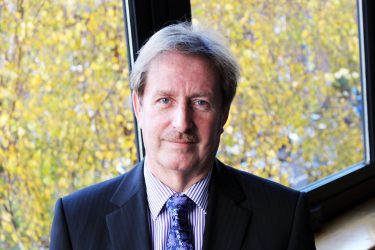
Robin Brown sales manager of Friedheim’s digital solutions divison
Building blocks
It is important to be realistic with Industry 4.0 or smart manufacturing. Smaller print companies are unlikely to require robotic arms and sophisticated conveying systems at this point. That doesn’t mean Industry 4.0 is irrelevant to them, though:
‘Moving your working premises into the “digital future” is an inherently expensive thing to do,’ said Stuart Bamford, national sales manager for post-press solutions at Friedheim. ‘A small printer or trade finisher isn’t going to need their entire finishing department to tie in with their MIS, but 2018 saw many of our customers automatically switch to the building block of the Industry 4.0 concept – data.
‘With the introduction of the GDPR guidelines, most of our customers re-evaluated their data and the capturing process, along with how they processed it. This is the first step to Industry 4.0, not simply for direct mail but for many other processes. The data is crucial to achieving the kinds of personalised products the industry has been craving.’
Heidelberg’s Anthony Thirlby agrees, pointing out that improvements generated by transparent factual and proactive data are ‘incredibly powerful tools’. While this article has drawn mostly upon the post-press sector of the print industry, where the intricacies of job format changeovers are most readily observed, the key to Industry 4.0 is software. Mr Thirlby is of the opinion that software will be ‘the heartbeat and foundation of any successful print-related business’, giving it the ability to react and scale up or down as customers require. ‘Through automated sequences and highly reduced touch points we are creating something that lets our customers concentrate on running their businesses, instead of worrying about output or performance.
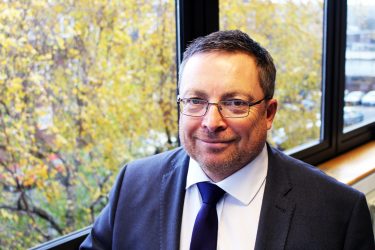
Stuart Bamford, national sales manager for post-sales solutions at Friedheim
Connecting and learning
In essence, the industry has been putting Industry 4.0-type integrations in place and showcasing them at trade shows for a number of years. As far back as drupa 2004 for example, PrintCity had an entire hall dedicated to a number of “smart factory” lines. The theory then, as now, was about communication from front to back, and JDF – the language by which print systems communicate – was a three-letter acronym that people puzzled about. It was important, but it was coming anyway; as a printer you did not need to know how to code it, nor did you need to go out and buy it; it took time to mature.
There is much more to come, of course. At drupa 2016, Duplo showed a DC-646 cutter-creaser integrated with HP’s Print OS software, providing continuous status and reporting information. Duplo says this brought the Internet of Things to its products for the first time in its cloud-based e-Tandem software. Duplo is planning to roll this software out across other products, meaning that more customers can ‘benefit from the increased power of connecting elements of the production chain and insight into the huge benefits it brings’.
Another element of the Industry 4.0 revolution will be machine learning, where machines such as stitchers and binders will remember adjustments made on-the-fly with historic jobs and will intelligently apply them automatically next time the job runs.
Industry 4.0 (and, for the print industry, the allied Print 4.0 and Finishing 4.0 terms) may be a buzzword, but what it stands for is the future of the industry. It informs the development of every piece of new technology that comes to the print market, so whether you know or care about it or not, it will be there eventually, quietly humming along in your production facility – providing somebody hooks it all up. Its influence will not be malign. ‘Companies that truly invest in Industry 4.0 are absolutely running lean,’ says Jason Seaber of IFS. ‘They are producing print in the most efficient way, and that makes you competitive.’