Itma, the international trade show for textile machinery, demonstrated how far digital textile printing for garments and home décor has come. Nessan Cleary reports.
This year we’ve seen textile printers at two shows – Fespa and Itma – both targeting different types of customers, but both fundamentally appealing to the same market and asking the same question: is there a viable market in digital printing of textiles?
Both shows have come at this from different perspectives. Wide format printers have been printing soft signage and very short run clothing – mostly adding corporate logos to workwear and sportswear – for over 10 years now. This is mostly done with dye sublimation technology on polyester-based fabrics and most of the textile printers that we saw at Fespa reflect this.
But Itma, which comes around only every four years, is a show about textile machinery for the established garment and decor markets, which are mostly looking at mass market high volume production, and printing – digital or otherwise – is only a small part of this. Consequently, most vendors showed much larger and more productive presses than at Fespa. More importantly, the trend is toward printing to natural fibres, particularly cottons, with most vendors demonstrating disperse and pigment inks.
Mimaki introduced a new version of its TX300P, which is a 1.8m wide roll-fed printer with two sets of ink lines and printheads so that it can be loaded with two different types of inks simultaneously. This allows users to switch back and forth between inksets depending on the job in hand. The original machine was designed to print direct to textiles, but the new one allows customers to choose between printing to transfer paper or to fabric, thanks to a new interchangeable platen. The printer can be configured with three different ink combinations, including textile pigment and sublimation transfer, or direct sublimation and sublimation transfer, with textile pigment and direct sublimation to come later.
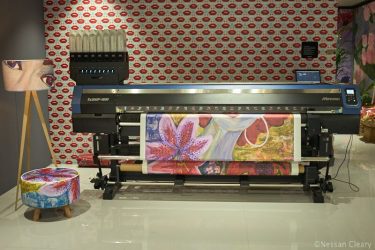
This Mimaki TX300P can be loaded with two sets of ink simultaneously and print to either paper or fabric
MS Printing Solutions, which is part of the Dover Digital Printing portfolio, showed off a new scanning printer, the Mini Lario. It takes substrates from 1.8 to 3.2m, with up to eight colours. It can be configured with two sets of CMYK for a maximum speed of 18.2m/min, dependent on number of colours and resolution, on both fabric and paper. It was shown with a new in-line fabric pre-treatment that should reduce setup times and allow it to print to uncoated materials.
The Bobst subsidiary Mouvent showed off a faster version of its textile printer with a new TX802. The heart of all the Mouvent printers is its modular printhead cluster, with each cluster having four Fujifilm Dimatix Samba heads. The original TX801 had two clusters, meaning eight heads in total. The main difference with the new TX802 is that it has four clusters, or 16 heads, doubling the speed of the printer to 100m/min. Both of these machines print a 1.8m wide image, and can handle woven, non-woven and knitted materials including cotton, silk and lycra. Currently there are reactive and acid inks available; disperse and pigment inks should be available in the near future.
Epson used Itma show to announce a new Monna Lisa Evo Tre 64 scanning printer. As with all the Monna Lisa printers it uses Epson’s own PrecisionCore printheads, in this case 64 of them, which deliver up to 779sqm/hr. This speed can be achieved with 600 x 600dpi resolution with two passes but the printer itself is capable of 1200dpi. It uses Epson’s Genesta acid, reactive, disperse and pigment inks.
The company also showed off an upcoming entry-level Monna Lisa printer, the Evo Tre 8, which has just eight heads. This can produce up to 265sqm/hr at 300 x 600dpi in a single pass, although multiple passes will produce better quality. It can be upgraded to 16 heads, though only at the factory.
Epson also announced the Genesta PG-Revo pigment ink series that’s said to offer high rub fastness and good print quality.
Kornit launched its Presto roll-fed textile printer, which does away with the need for both pre- and post-treatment. This is a 1.8m wide roll to roll printer that uses a new Robusto inkset complete with a water-based fixation solution. It’s a wet-on-wet process with the fixation acting as a binder, holding the pigment ink to stop it from spreading.
This allows the Presto to print to virtually any type of fabric, including natural and knitted materials, but it also means that the ink sits on top of the fabric and doesn’t penetrate into the fibres. This chemistry is complemented by the separate drying and curing unit, which circulates hot air to vaporise the water content and then cures the ink so that chemical particles within the ink bond the ink to the fixation and the fixation to the fabric.
Durst has introduced the latest version of its textile production press, the Alpha Series 5, in both the 190 and 330 versions, with the 330 version on show at Itma. Durst has made a number of improvements including a dual roll system that allows customers to run two rolls side by side, completely independently. It’s particularly effective when used with the larger 3.3m Alpha 330 and can significantly boost the productivity. Durst has also added a Super Multipass mode, which is said to give 30% better performance than comparable systems.
Durst also has a new advanced digital pigment ink for waterless one-step production that is said to have good light fastness and wet rub fastness and can be used on all types of fabric. It is optimised for printing without pre-treatment but Durst still recommends a pre-treatment to achieve the broadest colour gamut. There are eight colours in total – CMYK plus orange, red, green and blue.
There are several strands that make up the textile market, some of which will be easier than others for existing print service providers to enter. Certainly there are printers already using dye sublimation to tackle the sportswear market and at Itma several printers demonstrated good results on natural fibres with little or no pre- or post-treatment necessary. The other thing that was clear from Itma is that the digital printer vendors are all expecting to see massive growth in the textile market and have invested heavily in R&D.
This is partly because digital printing is a more sustainable way of producing textiles without the huge water consumption and pollution associated with more conventional methods. But it’s also down to growing willingness amongst consumers to order garments and décor online and to personalise them, which fits perfectly with the on-demand business model that most digital printers are used to. The question for service providers is whether or not they have the skills to tap into this growing market.