Sheet-fed electrophotographic presses continue to be the mainstay for many print service providers for short-run fast turnaround work on a variety of different media. Nessan Cleary surveys the market.
Toner-based digital production presses have been a staple part of a print shop’s armoury for the best part of the last 20 years. In that time they have proven their worth for producing short-run fast turnaround jobs as well as variable data. They’ve held their own against both offset and more recently inkjet technology, thanks to their ability to print to a wide range of materials without needing pre-treatment, as well as their ease of use and excellent image quality.
The market is still split between the heavy-duty beasts and the lower volume machines. Inevitably there’s less distinction between the light duty and mid-range machines as continual improvements mean that the lighter machines are extremely capable devices so that the choice largely comes down to the volume of work.
Thus the most recent production press, announced earlier this year, is Canon’s ImagePress C910 series, which is aimed at the lower volume end of the market. There are three models in this series, the C910, C810 and C710, producing 90, 80 and 70ppm respectively. They are designed to produce monthly volumes of 40,000 to 167,000 A4 pages but can handle monthly peak volumes up to 500,000 A4 pages. These printers have 2400 x 2400dpi resolution with a default 190lpi screening pattern. The image is printed to a transfer belt which features a soft elastic layer that helps to evenly distribute the toner across the media, even with textured and embossed substrates. They can handle stocks from 52 to 350gsm, though they will slow down for media over 220gsm.
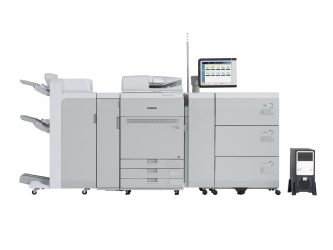
Canon’s ImagePress C910 series is a light production digital printer able to run at speeds of up to 90ppm
At the other end of the scale, Kodak introduced the Nexfinity, first previewed at Drupa 2016 and officially launched in March 2018. Earlier this year Matthews the Printers revealed that it had taken the first of these to be installed in the UK. It’s the latest generation of the Nexpress dry toner printer, with a new high resolution and multi-bit LED writing system giving 1200 x 1200dpi and 256 levels of exposure on the imaging cylinder. It should be capable of producing up to 152 A4ppm and handle standard sheets up to 356 x 520mm.
Christopher Riddell, managing director of Matthews, says the company tested a number of digital presses but found that the Nexfinity won out in terms of its print quality, which he says is better than offset, adding, ‘We can get much better definition in the highlight areas and the contrast.’
Indeed, most vendors have looked at ways to improve the overall image quality of their presses, and particularly the colour management over longer runs so that they can produce more consistent results.
Ricoh updated its production printers last year, starting with the flagship Pro C9200. There are two models in the series: the C9200, which can produce up to 115ppm A4 and average monthly volumes of 245,000 sheets; and the C9210, which runs at 135ppm A4, with an average monthly volume of 300,000 A4 sheets. Both have inline sensors for auto calibration and auto adjustment to improve registration plus Auto Colour Diagnosis technology that can detect and adjust subtle tone fluctuations while printing.
Konica Minolta has developed the IQ-501 module, which automates various colour control settings. It’s included in the AccurioPress C3080 colour series, as well as the AccurioPress 6136 monochrome range, both of which were launched last year.
HP sells a number of Indigo liquid toner presses but its main production model is the B2 format Indigo 12000HD. Last year HP added a new FM screening mode, Indigo HDFM, which places ink dots in a ‘random’ distribution, increasing the accuracy of ink dot placement, and eliminating the appearance of rosette patterns and moiré. This leads to sharpness in highly detailed images and halftone text applications.
Going beyond volume
However, although image quality is always going to be important, there are other factors at play, which reflects the fact that electrophotography is a mature technology and we expect even the cheaper presses to produce high quality images. But these days printers are also looking for features that will help them satisfy more applications. Most presses now can also print to longer sheets, handy for posters, dust jackets for books, or for producing tri-fold products such as menus or direct mail. So, even Canon’s new light production C910 series can also print single-sided banners up to 1300mm. Kodak sells an optional feeder for its Nexfinity and Nexpress ZX that allows for sheets up to 1.2m long and substrates up to 610micron thick.
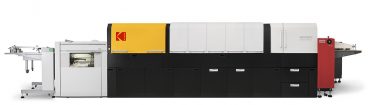
Kodak’s Nexfinity sheetfed press builds on its Nexpress platform
Several presses now offer a fifth colour station that can be used to expand the colour gamut or to add special effects. Mr Riddell of Matthews says that he has mostly used the Nexfinity’s fifth colour station for printing white, but has also experimented with mixing other colours, noting, ‘We’ve had pretty good results, especially for things like a limey green, where you would normally have to run a special colour.’
Ricoh offers its mid-production Pro C7200 in both four-colour and five-colour versions. Neil Kirbyshire, product marketing manager for Ricoh Europe, says that the C7200 appeals to both inplants and commercial printers with roughly a 50/50 split between demand for the two, but this changes to 80/20 in favour of the fifth colour if we just consider commercial printers. Mr Kirbyshire points out that commercial printers need to be able to satisfy as many potential applications as they can and the fifth colour can help with this. However, he adds that most printers use either white or clear toner in the fifth station: ‘When we start to get into some of the neon colours and expanding the colour gamut then I think that most people are still in the experimental stage as to what they can do and apply to their customer base.’
Xerox has gone a step further with its 130ppm Iridesse press, which has six channels for CMYK plus two channels for special effects such as metallic gold or silver. Depending on how you configure them it’s possible to print the metallic tints first with the colours on top, or you can put the metallic tint on last. The metallic toners are said to have both a high sparkle grade and high reflectance. The clear toner can be used to add spot varnish or textured effects to the overall design. There’s also a white toner that can be used to add spot effects. It can be layered under or over CMYK – or both for double impact – on a wider range of media including black, transparent or metallic stocks, craft paper, and synthetics and polys.
Xerox has also addressed the need for media flexibility, adding recently the ability to print on extra-long sheets up to 1200mm and can auto-duplex sheets up to 729mm in length. The press can run stocks from 52 – 400gsm and will take a variety of media including coated and uncoated papers, window decals, synthetic papers and polyesters. There’s a stock library that contains profiles and optimises settings such as fuser temperature specifically for each media.
Finishing flourish
Most vendors have also addressed the range of finishing options available for their production presses. Thus Canon added a new Document Finishing Device interface and bridge adaptor to its C910 series. This connects the finishing units to Canon’s own W1 staple and booklet finisher to create an inline solution. There are more finishing options, including a multi-purpose stacker for intensive banner printing, a continuous output kit for unattended perfect binding, and two booklet-finishing stations, including a compact version for sites with limited space.
This attention to finishing also applies to the black and white market, which has remained remarkably persistent despite the best efforts of most vendors to persuade printers to switch their monochrome work to colour. Ricoh has just introduced a new series of light production monochrome presses, the Pro 8300. The series includes five printers starting with a compact model aimed at office and education markets and running at 96ppm, with faster models designed for CRDs, print shops and commercial printers, with speeds up to 136ppm. All of these gain the latest iteration of Ricoh’s VCSEL (vertical cavity surface emitting laser) imaging engine with 2400 x 4800dpi resolution for smoother lines and gradations.
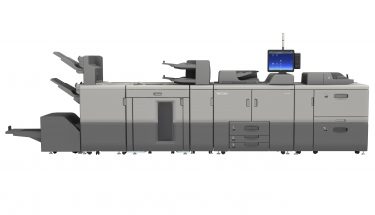
Ricoh’s Pro 8300 series of monochrome printers comes in three variations, with or without scanner
But Ricoh’s main reason behind developing this series was to create a more modular platform with more finishing options. Thus there’s a new booklet maker for the faster models that can handle up to 30 sheets at 80gsm at one time plus a new cover interposer with air assistance supporting coated media up to 350gsm. There are also two shift trays with a stack capacity of 4500 sheets, new trimming and long-sheet handling peripherals designed to support flexible ‘green button’ production.
All of these can handle one million pages per month, and are built to print 60 million pages over a standard five year contract. These new machines have been designed to handle peaks in production – up to four million pages per month in the case of the Pro 8320 – though not on a regular basis.
Inkjet has largely replaced toner in terms of web-fed digital presses and is beginning to appear in sheet-fed guises, something we’ll be looking at in a future issue of Digital Printer, but when it comes to mainstream commercial sheet-fed work, electrophotography still remains the technology of choice for short run jobs and those requiring high image quality and flexibility in choice of substrates. This in turn means that there is a greater emphasis on the type of jobs that can be run, particularly in terms of the substrates that can be used, as print service providers try to expand the range of applications they can satisfy. There has also been a noticeable trend towards inline finishing, which is essential to reduce the degree of costly manual intervention that would otherwise be needed, and suggests that printers are looking to automate more of their production to cut costs.