In the concluding part of this article, Michael Walker looks at Cloud software offerings for production and colour management and business intelligence.
Last month we looked at what the Cloud is, why you might want to consider it – or perhaps won’t be able to avoid it – as part of your software infrastructure. We discussed some specific examples that enable work to be acquired and allocated and company-wide systems to be managed, plus some services that can generate profitable print work as part of multi-channel campaigns. This time, we’re looking at solutions that sit closer to the production workflow itself and which complement MIS by adding Business Intelligence (BI) capabilities.
Cloud-compatible wide-format workflow
Large format workflow developer PrintFactory allows for jobs to be split across various software platforms and interconnects them via XML; this can be linked to cloud-based servers for management processes and file routing if desired but the heavy production processing is still done on the customer’s servers. XML tickets for job preparation and planning can be sent to and from MIS and web-to-print systems wherever they may be.
‘Assets could be held locally but the job settings generated centrally and the tickets sent to the [local] servers to work on the original files,’ says PrintFactory’s Toby Burnett. He adds that the software has been used to configure a complete ‘lights out’ Industry 4.0-certified workflow.
Colour and production management
Fujifilm’s only pure cloud offering is XMGF ColorPath, an online press calibration and profiling service that’s been around for a few years. This aims to simplify the task of keeping presses – both litho and digital – printing to specified colour standards by uploading test chart measurements and having a new profile calculated and sent back. The system was originally designed to keep presses within a specified tolerance of industry standards like the ISO 12647 family but Mr Davies says that it is also being used to meet users’ own house standards, particularly by owners of Fujifilm’s JetPress inkjet press which offers a wider colour gamut than the offset standard.
Fujifilm has also offered Pressero, a web-to-print platform from US developer Aleyant, which also offers three other cloud-based tools. One of those which is bundled in Pressero, though also used in some competing solutions, is E-Doc Builder, an online document design, personalisation and variable data printing engine. The others are T-Flow, an automated prepress workflow and PrintJob Manager which offers MIS-type features for job quoting, management and tracking.
T-Flow allows customers to deliver files via the internet for pre-flighting, proofing and correction. Once they are approved, T-Flow downloads print-ready files to the printer. ‘This happens behind the scenes, so it’s not a frustration [for users],’ says Aleyant president Greg Salzman, in response to the question whether bandwidth is an issue. He adds that about half his T-Flow customers integrate the system with their own production while the rest use it stand-alone. It is an option for customer to host the software themselves but many of these subsequently sign up for the fully hosted service.
Mr Salzman describes PrintJob Manager as ‘an integration hub that integrates over 1000 applications’. It’s not specific to print, covering applications like marketing automation and CRM, and ‘can broker connections between anything, for example, accounting and shipping management.’ It’s also available as a Zapier app, which allows it to link into the set of integrations supported by that environment, which he says can take you ‘80% of the way and make a bespoke conversation more practical’.
Mr Salzman says he’s seen a swing in attitudes from ‘nobody’s going to have my data’ to ‘the cloud makes it so easy’, perhaps because of the range of security options that the platform providers such as Microsoft and Google make available. That said, he quotes a customer who admitted to having made $1 million equipment decisions more easily than software ones. The intangible it seems, is ‘not as much fun to pay for’.
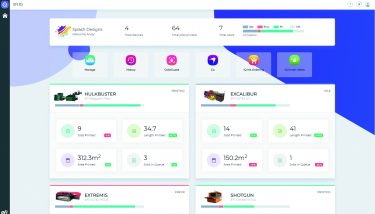
EFI IQ is initially focused on the company’s wide-format devices
Business intelligence
Heidelberg offers support for its presses and Prinect workflow and Smart Business Intelligence (BI) analysis capabilities via the cloud, on a subscription model, rolling out updates every 14 days. Head of software sales and service for Northern Europe Jacob Hededam points out that the subscription model is becoming prevalent in personal life, from TV and music streaming services to car leasing and explains how in print, lots of customers sharing data helps share the R&D and support provision costs, but it does rely on volume. He acknowledges that fear or lack of trust have been issues. ‘There’s still an old-fashioned mindset, but it’s moving slowly,’ he says. He adds that considerable effort has been put into not only meeting GDPR requirements for handling of European customers’ data, but that additional local requirements have also been met.
The BI offering has been available since the beginning of February but is being rolled out one country at a time, with UK availability scheduled for later in 2019. It allows insights into overall performance data that can help identify hidden bottlenecks, such as litho presses waiting for plates or paper, or jobs awaiting customer approval. With digital presses, it can help plan better times for scheduled maintenance. Once these hidden problems, usually focused around the press, are found, Mr Hededam says it becomes a ‘natural process’ to expand the data collection.
As part of this, Heidelberg announced in June that it has acquired German software developer Crispy Mountain, whose Keyline MIS has been cloud-based since its inception, and that this will play a key part in developing Heidelberg’s HEI.OS software platform which it plans to be open to other manufacturers. Mr Hededam commented, ‘The acquisition of Crispy Mountain was to bring on board critical cloud development resources. We were able to integrate the team from Crispy Mountain into Heidelberg for the long term in order to shorten the path to launching our products in the cloud ecosystem.’
Also aiming to bring an overview of a business, though initially aimed more at wide-format shops, EFI’s IQ cloud offering became available in June 2019. Available free of charge to EFI customers on the Enhanced Service Programme, it gathers printer data to compile statistics on up- and downtime, square meterage produced, ink consumption and errors. ‘There’s a multitude of functionalities and it will grow over time,’ says Chris Schowalter, director of EFI’s Fiery Market Segment Management. Immediately, it covers ink ordering, colour accuracy monitoring, driver and settings management and ‘intelligent’ pre-emptive maintenance and printer/profile recommendations to optimise ink usage or colour gamut.
IQ allows printers to connect directly to the cloud. Initially this includes the Pro hf100/25 wide-format machines, some Reggiani textile printers and the Nozomi corrugated press; these will be joined this summer by the Vutek 5r, GS and FabriVu models, to cover the complete EFI superwide range. Mr Schowalter says support for Fiery-driven toner presses is also on the cards, which will expand the applicability into mainstream commercial digital print and emphasises that it should be applicable to small print shops, though it also scales to support multi-location multimachine businesses.