Both sheet-fed digital presses and particularly wide-format inkjets can print on a range of materials outside their normal applications but may need some special handling. Simon Eccles explains
Paper is always the substrate most people associate with printing, unless you’re a signage or vehicle wraps printer, in which case you probably think of vinyl first, or a textile printer in which case it’s going to be natural or synthetic fibres. Either way, these common substrates are what the relevant digital printers are optimised for first and foremost. But out in the wider world of print, there’s often a requirement to print on less common ‘difficult’ materials, such as solid plastics, metals, wood, glass and leather.
We’re classing these as difficult because they may need special preparation, techniques or attention, though if you’ve got the right equipment, operators and experience, then they need not be difficult in reality. Many of these were originally printed by screen process (and a lot still are), but wide-format inkjet has been steadily moving into these applications for the past two decades.
Less obviously, except perhaps to their owners and operators, commercial digital print processes – dry toner, liquid toner (HP Indigo), UV inkjet and the newcomer Landa (Nanography) can print on many plastics and synthetics.
Wide-format inkjet options
Taking wide-format printers first, UV-cured ink was the only option for years. More recently the abilities of HP’s Latex and Mutoh’s MP31 resin ink to print on rigid media also enable work with these materials, given suitable primers.
The original way to apply print to metals such as aluminium composite, or wood, was to use solvent inks on self-adhesive vinyl that was then applied to the rigid media. However, the development of flatbeds with heavy duty handling systems allowed direct printing without the extra application stage.
Self-adhesive vinyl is still perfectly satisfactory for many applications, although it does alter the surface appearance, even if clear vinyl is used. Although it obviously involves an extra production stage, the vinyl can be printed by eco-solvent printers costing less than £10,000. An applicator table (costing from £10,000 to £20,000 for a good one) is desirable, though not absolutely necessary, for getting bubble-free finishes and a decent throughput. Large format UV hybrids and flatbeds for rigid media start around £50,000, although the small A3+ ‘baby flatbeds’ from the likes of Mimaki, Mutoh and Roland start at less than £20,000. You don’t need an applicator for these.
A solvent ink may readily print onto a metal or glass substrate, but as it cannot soak in, dissolve or soften the top surface, it cannot key into it to lock the pigment-carrying resins to the substrate. UV inks that react to ultra violet light to form cross-linked molecules which bond to each other and to the surface of the media do better, but even UV struggles with very smooth surfaces such as glass, some acrylics and metal.
Media manufacturers and converters may pre-treat or pre-coat the media to make it more ink receptive. Plastics and some papers can be electrically corona treated to increase their surface energy. If the material is supplied ready-treated it can be stored for several months before the effect gradually dissipates. In-site corona units are available for printers to refresh the effect.
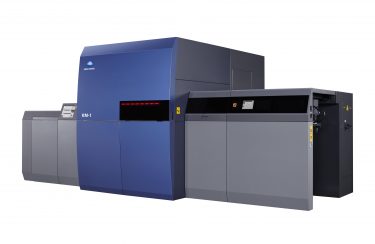
Konica Minolta’s KM-1 B2 inkjet uses UV-cured inks which means it can print on plastics
A primer primer
Corona treatment isn’t so effective for glass and metals, so if there are ink adhesion problems then a clear primer coating can be applied. This adheres to the substrate and forms an ink-receptive surface. Some inkjets (including the new HP Latex hybrids) can apply a primer directly.
Roland’s UK head of sales Rob Goleniowski, says, ‘Glass sometimes needs pre-treatment – it’s a very difficult surface to get durability on. You can treat it yourself or buy it pre-treated. For wood, Roland Eco-UV works fine, unless it’s something strange like balsa. The small drops don’t spread before curing, so no pre-treatment is needed.’
‘Mimaki sells a clear primer in a 500ml can, called GM1,’ says Richard Williams, showroom manager at UK distributor Hybrid Services. This can be applied by cloth, brush, roller or spray gun to difficult surfaces, he explains. ‘In the showroom we also use other primers, such as Sericol’s screen process primer for glass. What we’ve found is that not all glass is the same, for instance lead crystal is much harder to adhere to.
‘All our flatbeds have an option for a jettable primer that only goes under the ink image, so it doesn’t alter the surface appearance of the media. The jettable primer is more aggressive than the GM-1, suitable for more materials.’
Mr Williams agrees that wood printing has few challenges, saying: ‘No primer is needed for wood,’ but suggests that you might want to use white ink as an undercoat to bring the colours out, or you may want to get a colour tint effect with the wood grain showing through. ‘You can fiddle with multiple passes or turn the [UV curing] lamps down for matt effects,’ he adds.
Flatbed inkjets can only print on fairly flat surfaces, though these can be quite thick – head clearances of 50mm and even up to 200mm are quite common. The limitation for shaped surfaces (such as inset panels in doors) is the ‘throw distance’ of the inkjet heads, which is ideally only a few millimetres. The next step, still in its infancy, is ‘direct-to-shape’ UV inkjets which feature robot-controlled heads or media holders to adjust to some types of concave or convex surfaces. A few high profile bottle lines and tubular packaging printers use this.
Transfer processes
Another way to get print onto rigid media is dye sublimation transfer, or thermal toner transfer, both of which use heat presses to apply a printed image from a carrier sheet onto the final media.
Digital dye sublimation is often associated with textiles, but it also works very well for solids, as long as they are made from polyester or have a polyester coating. Objects can range from flattish phone covers to mugs to large aluminium display panels.
Dye-sub printers suited to solids (as well as polyester garment transfers) can be small and very low cost desktop inkjets, or larger wide-format models. Sawgrass pretty well dominates the small desktop sheet-fed printer market, but large format roll-fed inkjet options are offered by most manufacturers. The size limit for large objects such as wall panels is usually the availability of a suitable heat press – small A4 hand-pulled types can cost a few hundred pounds, but the largest ones need to apply hydraulic pressure and can cost tens of thousands.
Thermal transfers printed by dry toner digital presses (or desktop MFPs) are more versatile in that they work with many substrates without a special coating or primer, plus natural fibre textiles such as cotton, silk or wool. However, they don’t have as high a market profile as dye sublimation. The Magic Touch has made a particular speciality of thermal transfer papers and will also sell low cost OKI desktop printers (some of which can print white) and heat presses to go with them.
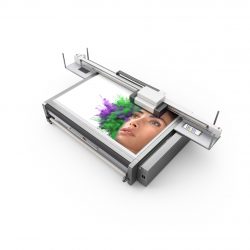
swissQprint’s flatbeds can handle a variety of materials but some may need priming, even for UV ink
Dry toner and feeders
Dry toner sheet-fed and continuous presses have always been able to print on some synthetics as well as paper, so these don’t really count as difficult media. Here the issue tends to be materials handling, rather than the ability to apply an image. HP Indigo’s liquid toner ElectroInk works with a surprisingly wide range of substrates, but HP has kept to conventional paper sheet and roll feeders, so there’s no facility for printing on rigid media. Way back at drupa 1995 the pre-HP Indigo company did demonstrate a special loader that allowed filled metal drinks cans to be printed, but this didn’t go into production. The flatbed HP Latex printers and the various HP UV flatbeds now do the job instead.
It may be a similar story for the two other commercial printer technologies that have potential for printing on a wider range of media. With limited numbers of installations it’s early days for both. Konica Minolta’s AccurioJet KM-1 B2 sheetfed press (also sold by Komori as the Impremia IS29), uses UV-cured inks and can certainly print on plastics as well as paper and cartonboard. However its sheet feeder and transport is basically a conventional Lithrone litho press system courtesy of Komori.
Landa’s Nanography offset inkjet technology also has the potential to print on virtually anything, including rigid and non-absorbent media. So far the only presses to be delivered have been the S10 sheet fed B1 carton configurations, either in simplex form for cartonboard, or in duplex form (as recently delivered to Bluetree Group’s Route One in the UK) for commercial double-sided print as well.
The chances are that the demand for difficult materials printing is low enough that the relatively slow flatbed inkjets are adequate for the volumes needed, so there’s no need to develop fancy heavy-duty rigid media feeders for higher speed presses. However, it may be worth considering the lessons of offset litho, where printing on plastics remained a rare speciality for as long as the UV curing systems were expensive and demanding to work with. Now that UV-LED and Low Energy systems are easier to fit at lower costs, with few drawbacks in use apart from ink cost, then the ability to print on plastics is just part of the product mix.
This may become the case for digital printing too, but in the meantime, if you’re faced with a ‘difficult’ material, chances are somebody else has already encountered it and there’s a process that can handle it.