Ink is an integral part of an inkjet printer so it’s vital to understand how that ink works to get the best out of a wide-format printer. Nessan Cleary explains
is to put graphical images on a range of different substrates, which could include anything from fabrics to PVC and metal. Those images have to survive the ambient conditions of wherever they are displayed, including outdoor weathering or interior retail spaces, and for a specified period of time that could be up to five years. The better the ink, the more reliable its performance, and since every wide-format printing provider depends on the things they’ve printed staying printed, it’s important to be sure that you’re using the right ink for the range of applications you’re offering.
That said, there’s rarely much choice of ink with inkjet and you’ll mostly have to use whatever the printer vendor supplies. This means that the ink is one of the most important components of a printing system to test when buying a printer.
Most inks will be tuned for a specific printer so that the manufacturer will have chosen an ink that’s suitable for the printhead in use and then tweaked the formula to improve jettability as well as playing with the temperature around the head to control viscosity. Printheads work best with low viscosity fluids but this characteristic limits the performance of the ink once it hits the substrate, where we want the ink to form defined dots. Consequently, most inks contain a highly complex mix of various additives, such as humectants to ensure the ink does not dry out in the nozzles, as well as binders to attach the pigments to the substrate.
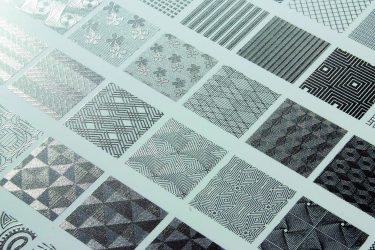
Mimaki’s MUH-100-Si silver ink can be used to produce various textured effects.
So what should you look for in an ink? Obviously the inkset has to be able to reproduce a wide range of colours. Most people test this against the Pantone range but you should also consider specific customer logos as well as tricky colours like rhodamine red and reflex blue.
Naturally the ink has to be scratch-resistant. Generally, flexible UV prints (on roll media) will not cure to the same degree of hardness as some flatbeds so if for example you’re printing rigid boards on a hybrid machine then you will want to be sure that the cured ink can withstand the level of abrasion it’s likely to encounter. This also applies to indoor prints such as wall coverings that might encounter a certain amount of abrasive cleaning chemicals. However, some vendors do offer a choice of inksets, which might offer better adhesion to some materials or a tougher finish for use with rigid substrates.
On a roll-to-roll printer the ink has to dry before it gets to the take-up roll. On some substrates you might struggle to lay down enough ink to reproduce vibrant colours without overwhelming the drying system. To counter this, some inks have a high pigment loading but this pushes up their cost; this is a worthwhile compromise if it allows drying – and therefore printing – at higher speeds.
Solvent, latex or UV?
At its simplest, most ink consists of a low viscosity liquid carrier that allows the ink to be jetted through the printhead nozzles, plus the pigment particles and some form of binder to attach the pigments to the media.
In the case of solvent ink, the solvent not only acts as the liquid carrier but also helps to soften the surface of the substrate so that the pigment can penetrate into the material, making it more durable and more resistant to weathering and scratching. The solvent then evaporates away into the atmosphere, leaving the dried pigment behind. Health and safety regulation has outlawed the most aggressive solvents (containing volatile organic compounds or VOCs) so that today’s eco-solvent inks generally work best with coated media. The printers need some drying to help speed the evaporation to dry the prints.
Eco-solvent is a relatively simple ink technology, which dries reasonably quickly so that both the printers and the ink are fairly cheap and still widely used. The major disadvantage is that you’ll have to wait, usually overnight, for the inks to fully dry before laminating, and for any odour to disappear. Suppliers such as Epson, Mimaki, Roland DG, Oki and Mutoh offer eco-solvent printers.
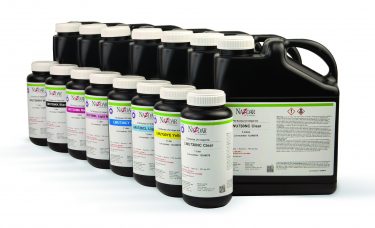
Nazdar has released these 730 Series UV inkjet inks, which are suitable for a wide range of wide format printers.
Latex ink – mostly associated with HP but also available from Ricoh – doesn’t actually contain latex but is instead a form of resin ink where a polymer is used to encapsulate the pigments, which are then suspended in water as a carrier liquid that can be jetted through the printheads. Once jetted, this ink relies on heat being applied, both to evaporate the water away, and to activate the polymers to bind the pigments to the media.
The major advantage of latex over solvent ink is that the prints are dry as soon as they come out of the printer with no need to set them aside for degassing. There’s no smell, which makes them suitable for use in retail as well as hospitals and schools. They are generally tough enough to survive outdoors unlaminated for up to three years, and longer if laminated. These inks are often seen as more environmentally-friendly than other inks, particularly solvent, because the main carrier liquid is water. However, it’s worth noting that they do require a lot of energy to cure.
Mutoh has developed an interesting alternative, with a resin ink for its ValueJet 1627MH hybrid printer that uses a solvent as the liquid carrier. However, unlike a latex ink, the resins in this ink are not heat activated. Instead it’s the evaporation of the solvent that causes the resins to bind to the substrate.
UV-curable inks rely on a chemical reaction, known as photo polymerisation. This polymerisation is triggered by photo initiators within the ink, which produce free radicals when exposed to UV light. The major components of these inks are monomers and oligomers, which the free radicals cause to cross-link together to cure the ink. UV inks are quite complex and require expensive raw materials, especially the photo-initiators that are used to start the curing process, so that these inks are always going to cost more than their solvent or latex counterparts. However, they are hard-wearing and can be used in many outdoor applications without further lamination. Moreoever, since they dry straightaway, they can be finished and delivered right after printing. UV-curing printers are offered by a wide range of printer manufacturers including Agfa, Canon/ Fujifilm, Durst, EFI, HP Scitex, Inktec, Mimaki, Mutoh, Ricoh, Roland DG and swissQprint.
The conventional approach has been to use mercury lamps located on the print carriage to provide the UV light but many vendors are now turning to LEDs as an alternative. There are numerous advantages to these, including the fact the LEDs will in most cases last for the lifetime of the printer, and use significantly less energy. But LEDs produce only a narrow range of wavelengths so the ink has to contain a photo-initiator that responds to the precise wavelength of the LED in use. This of course pushes up the price, though economies of scale mean that this is less of an issue now that this curing approach has become so widespread.
Several vendors offer additional colours, with white being the most common. White ink relies on larger, heavier particles, typically titanium dioxide, which sink to the bottom of the ink tanks. It’s essential that the ink system routinely stirs the ink to prevent this, ideally also recirculating the ink through the ink system to keep the particles in suspension. Not every job requires white ink, so there’s a danger the ink might dry in the heads, but many jobs, such as backlits, do require a white layer so you may be better off with two white channels to maintain the speed of the printer while still achieving the desired opacity.
There are also special effects inks, such as metallic. Mimaki, for example, has developed a metallic ink, MUH-100-Si, for use with its UJF-7151plus industrial flatbed printer. As with white ink, the heavier particles tend to sink to the bottom of the tank but the UJF-7151plus uses printheads with built in recirculation. This ink can produce a reasonably wide range of different metallic tints by printing coloured ink on top of the metallic ink. The metallic ink can also be combined with a clear ink to produce textured and embossing effects.
Several ink manufacturers offer aftermarket inks, which can offer cost savings of up to 30% compared to the printer manufacturers’ offerings. These inks will usually be designed to work for a given printhead but won’t have been tuned specifically for any particular printer. There are quite a few solvent inks available but not so many UV inks, mainly because the raw materials for UV inks tend to be expensive and UV printers are more expensive than solvent machines, so that the ink is not such a big part of the total cost of ownership.
Inevitably, an aftermarket ink will almost certainly void any warranty on the printer. Given that most wide format printers will come with a two-year warranty, the printer should have more than earned its keep by the time the warranty expires. So for a lot of service providers it makes sense to use the vendor’s ink for the warranty period and then to switch to a third party ink to squeeze a bit more margin out of the printer before ultimately replacing it.
Finally, it’s worth noting that most RIPs will have some degree of colour management and this should allow you to minimise the amount of ink that’s laid down without compromising the colour density. This will not only save money by using less ink, but will help ensure the ink dries quickly.