One way to add perceived value – and therefore production margin – to print work is via enhancement and embellishment, whether that’s done in the press or via a separate process. Michael Walker looks at the options for digital finishing
There’s one area in which the electronic screens which increasingly occupy our attention can’t compete with print, and that’s finishing that’s done for aesthetic effect. Foiling, spot UV, metallic substrates or inks, fluorescent colours and raised texture effects all add novelty, invite physical interaction and instil a sense of intrinsic value that can’t be matched on a phone, tablet, laptop or high-resolution display.
While all of these treatments originated in staunchly analogue processes that are still in widespread use, digital printing technology and techniques have evolved and adapted to bring the run-of-one every sheet different capability to finishing. It does this in a number of ways, some of which mimic traditional post-press working and some of which move key elements into the printing process itself. In this article, we’ll look at the post-press options.
Print then finish
Post-press embellishment divides into fully digital approaches in which every sheet can be treated differently, sometimes with multiple options simultaneously, and analogue ones that are optimised for the short runs typical of digital print.
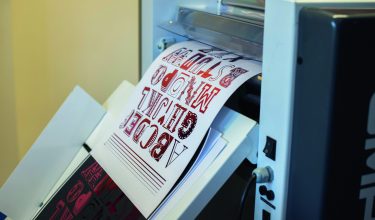
Banner output can be handled by GMP as well as standard SRA3
There’s also the hybrid press-and-laminator approach found in foil-over-toner systems such as those supplied by Caslon and Vivid with its Matrix laminators. These involve multiple steps: print CMYK, laminate, print a black mask for the foiled area, then laminate foil onto second print layer. The heat in the lamination makes the black toner become sticky so that the foil adheres to it. The process can produce fully variable results but is labour intensive, though a wide range of foils is available for different colours and effects. It’s cheap, not requiring additional equipment beyond a suitable laminator, but the lamination may limit stock choices.
Another option in this category is GMP ‘sleeking’, a process that enables a wide range of holographic, gloss spot, matt and metallic effects to be layered onto digital print, but without the need for lamination first.
Robyn Turner, marketing director at GMP supplier Gardiner Graphics Group, commented, ‘The last eight months of the pandemic have no doubt been a challenging time for small format creative print. Nevertheless, we have seen some ingenious creativity from our customers using GMP Sleeking to create some truly dynamic solutions. There was a clear drive from printers to want to get more out of the solution, experimenting with different finishes and techniques. We launched Sleeking Collections in September as a way of servicing this demand.’
The Collections are a series of colour combinations of foils in shorter roll lengths for a lower cost, allowing printers to try effects and colours in a more affordable way. Gardiner is also opening an online shop for the sleeking foils and other finishing films.
Spot the difference
Digital ‘spot-UV’ uses dedicated inkjet printers that print a clear ink that dries to a gloss or sometimes matt finish. A good example is Duplo’s DuSense unit, which also offers texture-building options via multiple passes. Now upgraded to Pro configuration with an additional corona unit, the DuSense can handle a wider range of stocks and there’s a barcode unit to help match the spot UV ‘print’ to each printed sheet automatically. Duplo has also introduced the DuSense Digi Foiler, which uses the foil-over-toner technique on top of the clear UV to give a 3D foiled finish.
True digital foiling also exists, and is generally delivered by high-end dedicated ‘embellishment presses’ that apply foil variably to print, usually in addition to other effects, including spot UV. Two of the best known players here are Scodix and MGI. The former, distributed in the UK by Friedheim, has recently revamped its range into six models (see news, page 10), which offer different combinations from the Scodix repertoire. Supporting sheet sizes up to B2, these include texture and spot varnish functions as well as a variety of foiling types including holographic, which Scodix says provide equivalents for conventional lamination, embossing and hot foiling.
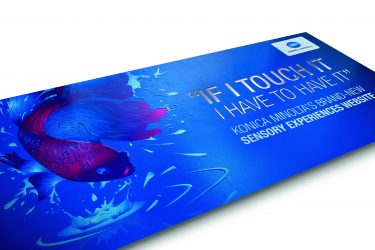
The MGI line of dedicated enhancement presses can add both textured spot UV and foiling on top of it
A dedicated ‘enhancement DFE’ for the Scodix machines was introduced this summer to provide greater throughput. Friedheim also offers the Komfi Spotmatic UV and foil-overtoner machines, the latter now including an anti-static bar, and the Kama DC76 Foil, which although principally aimed at carton production, offers effects such as embossing/ debossing, bejewelling and holographic plaques and labels, as well as cutting/creasing. It’s said to work well with output from Indigo 12000, Xerox iGen, Fujifilm JetPress and Konica Minolta KM-1 presses.
MGI is part-owned by and exclusively sold through Konica Minolta. Its range goes from SRA3 to B1 in sheet-fed and there’s also a 420mm roll version for labels and flexible packaging. The functions supported range from spot varnish only to tactile varnish to digital foiling. KM claims that high throughput is a differentiator, with the B2 JetVarnish 3D running at up to 3123sph, while the B1 JetVarnish 3D Evo can deliver up to 2291sph on stocks from 135 to 800gsm and can mix flat and textured varnish elements in a single pass. Raised elements may be up to 232µm in thickness.
Autobond has offered inkjet-based spot UV devices since drupa 2012, and since 2016 supports sizes up to B1. This year’s postponed show would have seen the launch of its first system with inline foiling capability. The range is available both as stand-alone embellishment machines with Heidelberg feeders, or inline to Autobond laminators, which VP of sales Oran Gilmore says is increasingly popular, adding, ‘From inception, we had always envisioned running in-line with our laminators to provide customers the ability to laminate, inkjet spot UV (either flat or raised UV), with the option of foiling all in one system.’
The systems can run at up to 60m/min and the UV varnish can be printed at 360 or 720dpi at thicknesses between 2 and 24µm, to simulate a conventional UV look or more textured or high gloss finishes respectively. The foiling aspect is also digital, with both hot foiling similar to MGI’s or cold foiling like Scodix’s running on the same unit.
Autobond MD John Gilmore explained that although the machines can foil over laminate, most book publishers prefer the foil to be under the laminate, so the company built a machine that does spot varnish, foils and then laminates. The Autobond 76 supports B2 landscape (75 x 53cm) and can be located at the infeed or delivery end of the line. Most jobs can be set up in around 10 to 15 minutes.
Kurz offers Digital Metal, a set of foiling technologies designed to work with digital presses, either laying foil down first for overprinting via inkjet, or using foil-over-toner techniques that work with either dry toner or HP Indigo Electro-Inks via its DM-Luxliner. A variety of foil colours is offered, together with ‘diffraction’ and hologram types, plus a clear option. The larger DM-Maxliner handles sheets up to B1 in size and offers both 600dpi UV spot coating and metallisation at up to 40m/min with both flat and raised / embossing effects available.