Book binding and booklet-making are some of the most challenging post-press tasks. Fortunately a whole host of companies offer top-of-the-range equipment and processes to get the job done. Charlie Kortens explores some of the options
Ashgate specialises in supplying short-run digital print finishing systems. It remains the UK distributor for the Finnish Fastbind range of machines, including the latest generations of Pureva Neo and Pureva Smart technology.
The Pureva Neo offers an all-in-one solution for high quality PUR and EVA book production. Available for under £8000, Ashgate describes it as an ‘attractive investment for any print shop to take advantage of PUR technology whilst also having the option of EVA hot-melt binding in the same machine.’ It is an all-in-one manual binder for all binding needs including soft- and hardcover books for higher margins and a versatile product range, tear-off pads with no adjustments for forme, size or paper type. It also comes with a new patented glue mechanism which has been developed to be easily cleaned or changed.
Meanwhile, the Pureva Smart PUR and EVA binder is being marketed as ‘the latest innovation for on-demand and short run digital finishing.’ It is a semi-automated binder that Ashgate considers the natural successor to the Fastbind Pureva XT, launched six years ago. Available at £15,000, the Pureva Smart is designed to meet the demands of customers who want ease of operation, consistency and speed.
‘In just a few years PUR binding has become the de facto standard for short run book binding,’ says Lewis Price, managing director at Ashgate. ‘Short run soft- and hardcover books have become one of the most profitable products a printer can offer. This means that as runs of on-demand perfect bound and hardcover books get shorter and shorter, printers are choosing to bring this type of work in-house due to time constraints, more control and eliminating set up and transport costs. At the same time, customers realise the benefits of PUR binding for the strength of bind and improved quality.’
The Pureva Smart and the Pureva Neo both work well in conjunction with the Casematic A46Z, Fastbind’s first semiautomated cover maker. This opens up the possibilities of producing personalised covers for books and albums as well as restaurant menus, ring or conference binders, luxury cases and more from A6 to 45 x 45cm.
Duplo describes its perfect binders as being built for a large variety of commercially produced products, leaning towards the digital print sector. When it comes to EVA perfect binding Duplo offers the DB-290 hotmelt perfect binder for creating perfect bound, tape bound and padded books. The machines can produce up to 200 books per hour at sizes up to 320 x 400mm and a maximum thickness of 40mm. Glue warm-up takes 30 minutes, but in standby mode, this is reduced to five minutes.
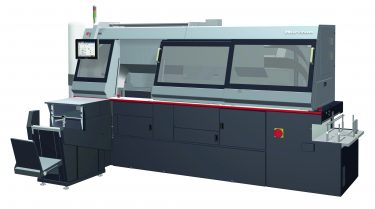
IFS now supplies Horizon’s BQ-500, which builds on its predecessors, the BQ-470 and 480
There is also the DPB-500 DuBinder, a fully automatic machine with a single clamp design and a maximum production speed of 525 books per hour. The DPB-500 includes sensors within the book clamp that measure each book’s thickness compared the correct version, with errors then being flagged to the operator. Duplo says that the DPB-500 is particularly sought-after for short-run production thanks to the reduced time for makereadies and the way it can successfully handle output from both offset and digital devices. It can also be fitted with a barcode reader for both the book block and the covers.
For PUR binding, Duplo offers the PFI Bind 6000 PUR and Duo machines. Both have complete automation with in-line scoring, and cover feeding as standard with a speed of 600 cycles and up to 300 books per hour. These are intended to be the ‘ideal solution’ for a printer who has litho and digital presses and is producing mid to high-volume production runs. The difference between the two is that the PFi Bind 6000 Duo enables the operator to select between PUR and EVA glues, whereas the PUR-suffixed model supports PUR only.
There is also the PFi Bind 2100 PUR, which helps printers to bring in-house the highly profitable short-run on-demand jobs that might previously have been outsourced. Through automation, each book is automatically measured and the amount of glue on each book block is intelligently applied, reducing errors and the cost of reprints. With its closed tank system, the 2100 applies the minimum amount of glue required via its patented re-circulation system. The company also recently launched the 150 Booklet System, a pairing up of the company’s existing DSC-10/60 feeding system and its DBM-150 Booklet Maker and Trimmer.
In 2020 Friedheim became the exclusive distributor of Hohner stitchers and stitching heads in the UK and Ireland, meaning it now represents all the manufacturers in the Post-Press Alliance in the two countries. Part of the agreement will see Friedheim supplying Hohner’s
new HHS Futura, a ‘puzzle-like’ hybrid stitching machine. This machine is available in multiple different configurations and can be extended or adapted to suit the customer’s needs. Depending on precisely how it is set up the machine can also deliver savings in terms of reduced energy usage and environmentally harmful emissions. Hohner also says that it takes up less space and requires fewer operators than competing machines.
The Futura incorporates a stitching unit with automated wire length and thickness adjustment, including stitching leg, via a 15-inch colour touchscreen with intuitive and non-text design and a trimmer allowing a B4 final format with optimum trimming quality. In terms of feeding units, there are four options to choose from and/or combine, including a cover feeder, a horizontal feeder, vertical feeder and a compact plano sheet feeder. The machine can also incorporate digital finishing options, folding and stitching capabilities, cross-folding and collating towers, including technology from other members of the Post-Press Alliance.
Speaking about the wider deal with Hohner and the PostPress Alliance, Friedheim managing director Mark Bristow commented, ‘At Friedheim, we take pride in the fact that we only take on the very best manufacturers in the world. Hohner are the leaders in this field and are the best at what they do. They are a highly motivated company with a brilliant track record of design and development, bringing the very best of their technology to market. The Hohner range complements our existing manufacturers perfectly, especially regarding the Post Press Alliance, and we’re looking forward to a long and fruitful relationship.’
IFS is now supplying Horizon’s new BQ-500, a fourclamp perfect binder that features a number of design and operational enhancements as well as support for the company’s IceLink automation and workflow software.
The new binder builds on its predecessors, the BQ-470 and 480, to enable socially distanced operation and reduced touchpoints while supporting a broader range of run lengths. Providing that book thickness does not vary by more than 5mm from one book to the next, the BQ-500 can bind 800 books per hour, dropping to 550bph if the difference is 64mm and 660bph with a 30mm variation.
‘This latest evolution of Horizon’s highly successful series of four-clamp binders elevates automation and ease of use to new levels supporting greater productivity and efficiency,’ says Eric Keane, IFS managing director. ‘Horizon’s team of engineers have reviewed and enhanced every element of the system from job input to delivery. Among the improvements are deeper scoring for a thicker cover, a new gluing mechanism, glue overflow detection, a faster nipping changeover and a switchable exit mechanism for thick book or PUR book production. The powerful combination offers any bindery a future-proof system for high quality and versatile service delivery.’
Able to produce those 800 books an hour with only a single operator, the BQ-500’s modular options include book block feeders for loose leaf book blocks or glued or sewn book blocks, in-line end sheet feeder and gauze feeder, cover slitting, barcode cover to book block matching and the ability to expand to a Smart Binding System with automatic roll and/or sheet fed inputs, in-line variable book trimming with zero make ready to enable book of one production on demand.
IFS technical sales director Jason Seaber adds, ‘The Horizon BQ-500 Perfect Binder sets new standards in design with increased automation, increased book-of-one productivity and increased quality control for a wider range of substrates regardless of run length. The Horizon BQ-500 is modular by design and can be expanded into a complete Smart Binding System with roll feed and/or book block feed inputs with in-line variable book trimming options, such as the Horizon HT-1000V zero make ready variable three-knife trimmer that can trim single or multiple books at a time, or the New Horizon HT-300 automated variable book trimmer designed for lower book volumes with the ability to also trim softcover books with flaps.’
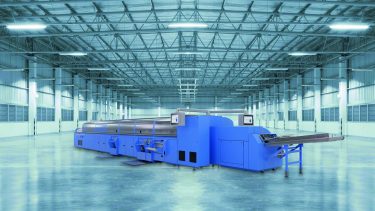
Müller Martini’s Publica Pro, suitable for magazines, catalogues and high-volume publications
One of the flagship offerings from Morgana is the DigiBook 300 XL Pro PUR binder, the latest device in the DigiBook range. With SRA3 press manufactures increasingly offering long sheet capability, this device takes those sheets and gives users the ability to produce landscape format books with spine thickness of up to 50mm. It can be used to bind large format photobooks, as well as short print runs of novels, account and legal documents, drawing pads, university theses and sudoku pads, amongst others.
The previous version required a three-phase power supply, which limited its installation to larger print shops and factories. The 300XLPro is a 32-amp single-phase machine, allowing for its installation in most commercial premises and print businesses.
Optional features on the new DigiBook 300XL Pro include a gauze station, which allows for the production of book blocks ready for case binding. In addition, users can opt for a high-capacity paper chip extractor, which may be useful for customers producing longer runs. The unit has a 78l capacity for paper dust, allowing long uninterrupted runs of even the thickest books.
The machine is also equipped with the same hermetically sealed PUR glue application system as its predecessors, has fast start-up and shutdown and minimal wastage, as well as automatic cleaning and sealing of the head at the end of the production run.
Other models available in the range include the DigiBook 200, designed for short to medium print runs, and the DigiBook 450, ideally suited to litho and digital printers who require medium to long runs of PUR perfect-bound books to a professional standard.
The company also offers the BM5000 series of bookletmakers. Available in multiple versions depending on customer’s exact requirements, the BM5035 and BM5050 machines feature two maintenance-free staple heads, and the BM5035s and BM5050s come with two or four stitching heads. These new systems are engineered for midto-high volume customers with features exclusive to this class.
Swiss company Müller Martini has long been a player in this market and continued to innovate in 2020, releasing the Vareo Pro, a three-clamp perfect binder, as well as unveiling a new generation of its Publica Pro perfect binders. The Vareo Pro, which is capable of 1350 cycles per hour, is an enhanced version of the company’s Vareo model, with new features including a new graphical user interface and what Müller Martini is calling a ‘unique operating concept’ developed to be ergonomic.
Compared to its predecessor the Vareo Pro’s hot-melt back gluing unit has been updated, and is also available with an optional trolley, making the two systems easy, reliable and, thanks to a separately available preheating cable, interchangeable without any loss of time. The hot-melt spine gluing system, which is based on Müller Martini’s Alegro 7000 cycle perfect binder, has also been completely redesigned to ensure good glue flow and temperature control. It is equipped with two application rollers and a separately heated counter-rotating spinner roller. The two roller systems are now independently height adjustable and edge gluing is now fully automatic as standard.
Müller Martini also says it has updated the Publica Pro because ‘even though softcover products are no longer printed in runs of hundreds of thousands or even millions of copies as they were a decade ago, high performance perfect binding is still very important.’ Described as ideal for magazines, catalogues and high-volume publications, the machine is available in three difference performance classes, capable of 12,000, 15,000 and 18,000 cycles per hour.
In addition, Müller Martini also launched the Prinova, a new saddle-stitcher designed for medium-length runs and capable of 9000 cycles per hour. Described as the little brother of the company’s existing Primera machine, the Prinova is being marketed as a ‘digital-ready system,’ for existing or prospective digital printing houses.
The system’s feeding stations have been redesigned so that it now boasts individual feeders with servo dives. It is also capable of holding up to 14 individual tiltable feeders and Müller Martini adds that it has made several technical improvements to the Prinova’s three-knife trimmer. All of this combines to allow for much faster changeover times, allowing the Primera to handle short runs more efficiently.
Perfect Bindery Solutions (PBS), based in Witney, Oxfordshire, is an importer of a range of products and machines that can be incorporated into digital binding lines. A key part of this offering is the Risetec automated perfect binding line, with a choice of one, four or seven clamps and the option to run with a Risetec or other make of three-knife trimmer downstream. Alternatively, PBS can supply an IML automated binding line to combine perfect binding, backlining/end-papering and three-knife trimming with variable sizes on the fly at 1250 books per hour with the four-clamp model. For one-offs and short runs there’s also the semi-automatic single-clamp IML BR3-PUR with PUR application for spines plus side hotmelt for manually-applied cases.
PBS also offers thread sewing through the Smyth range. These can run nearline or inline to a binder, with various levels of automation and speed, all able to handle really large books if needed, with spines up to 510 or 520mm long. Smyth’s Digitaline combines buckle folding, collecting into signatures for cross-folding, then thread sewing, while the Digitaline Plus is a hybrid system able to mix digital and litho printed sheets up to 500 x 700mm (and optionally 1000 x 700mm). It can also collect and fold only and eject to a conveyor for separate wire saddle stitching.